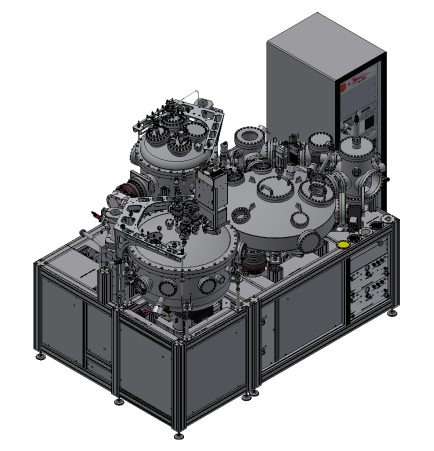
P453 – 4″ UHV sputter deposition cluster tool PTB
Application
UHV sputter deposition cluster tool for thin film and multilayer deposition at 4″ substrates
Year of delivery
2017
Installation site
PTB, Berlin, Germany
Design Features
- UHV magnetron sputter deposition cluster tool with combination of confocal and face to face sputtering.
- In two sputter chambers up to eight magnetrons can be installed.
- Deposition uniformity better than 5% in both chambers.
- One 2″ magnetron and upto three 6″ magnetrons can be used in face to face configuration in one chamber (called SP3).
- Upto four 2″ magnetrons can be used in confocal configuration in one chamber (called SP4).
- All confocal 2″ magnetrons with manual in situ tilting.
- Fully motorized 2 axes sample manipulators with integrated sample clamping stage and sample temperature stabilization (mild cooling and mild heating).
- Oxydation chamber with static oxydation pressure.
- Load lock chamber with lamp heating stage and ion source for sample precleaning and mild etching.
- Automatic sample transfer between all chambers via a radial distribution chamber.
- Integrated bake out system.
Special Features
- Radial distribution chamber is prepared for adding a third deposition chamber.
- At least two different sample sizes (4″ and 3″ wafer) can be handled (using different kind of sample holders).
Outer Dimensions
Technical specifications and performance values
General
Face to face sputtering chamber
Size
About 800 mm diameter, about 730 mm height
Material
stainless steel
Confocal sputtering chamber
Size
About 600 mm diameter, about 700 mm height
Material
stainless steel
Load lock chamber
Size
About 250 mm diameter, about 440 mm height
Material
stainless steel
Oxydation chamber
Size
About 200 mm diameter, about 300 mm height
Material
stainless steel
Radial distribution chamber
Size
About 1000 mm diameter, about 450 mm height
Material
stainless steel
Vacuum
Face to face sputtering chamber
Base pressure
< 3 * 10-8 mbar
Pump down time
1 hour to < 10-7 mbar
Chamber pumping
Cryo pumping stage, chamber lid differentially pumped by dry foreline pump
Bake out
< 120°C
Confocal sputtering chamber
Base pressure
< 3 * 10-8 mbar
Pump down time
1.5 hours to < 10-7 mbar
Chamber pumping
Turbo pumping stage, chamber lid differentially pumped by dry foreline pump
Bake out
< 120°C
Load lock chamber
Base pressure
< 10-7 mbar
Pump down time
0.75 hours to < 10-7 mbar
Chamber pumping
Turbo pumping stage with dry foreline pump
Oxydation chamber
Base pressure
< 10-7 mbar
Pump down time
1.5 hours to < 10-7 mbar
Chamber pumping
Turbo pumping stage with dry foreline pump
Bake out
< 120°C
Radial distribution chamber
Base pressure
< 10-7 mbar
Pump down time
1.75 hours to < 10-7 mbar
Chamber pumping
Turbo pumping stage with dry foreline pump
Manipulator features
Face to face sputtering chamber
Sample size
diameter max. 4″ substrate
Motion axes
2 motorized axes (manipulator arm rotation and z translation of the sample stage)
Sample clamping tool with motorrized sample release unit (part of the manipulator head) for optimized thermal contact
Temperatures
-10°C up to +70°C at sample
Confocal sputtering chamber
Sample size
diameter max. 4″ substrate
Motion axes
2 motorized axes (continous sample rotation and z translation of the sample stage)
Sample clamping tool with motorrized sample release unit (part of the manipulator head) for optimized thermal contact
Temperatures
-10°C up to +70°C at sample
Sample preparation features
Load lock chamber
Thermal treatment
max. 180°C at sample (no temperature regulation)
Plasma treatment
max. 10-3 mbar partly ionised argon gas (using a griddless ion gun)
Ion beam etching /
sample precleaning
Variable ion source to sample distance
Wide range variable ion energy and ion beam current
Oxydation chamber
Static oxydation pressure
0.6 mbar up to 1000 mbar
Smallest pressure step
0.6 mbar (gas inlet valve open for 1 s)
Pressure increase time
20 s for max. pressure